Electrical Discharge Machining (EDM) is a precise, non-traditional manufacturing process that removes material from a conductive workpiece using controlled electrical sparks. This innovative technology has revolutionized the fabrication of complex shapes and intricate features, particularly in hard-to-machine materials.
Key Takeaways |
---|
EDM uses electrical sparks to erode material |
Achieves high precision and complex geometries |
Ideal for hard, conductive materials like titanium and hardened steel |
Three main types: Sinker EDM, Wire EDM, and Small Hole EDM |
Offers advantages like machining intricate details and minimal mechanical stress |
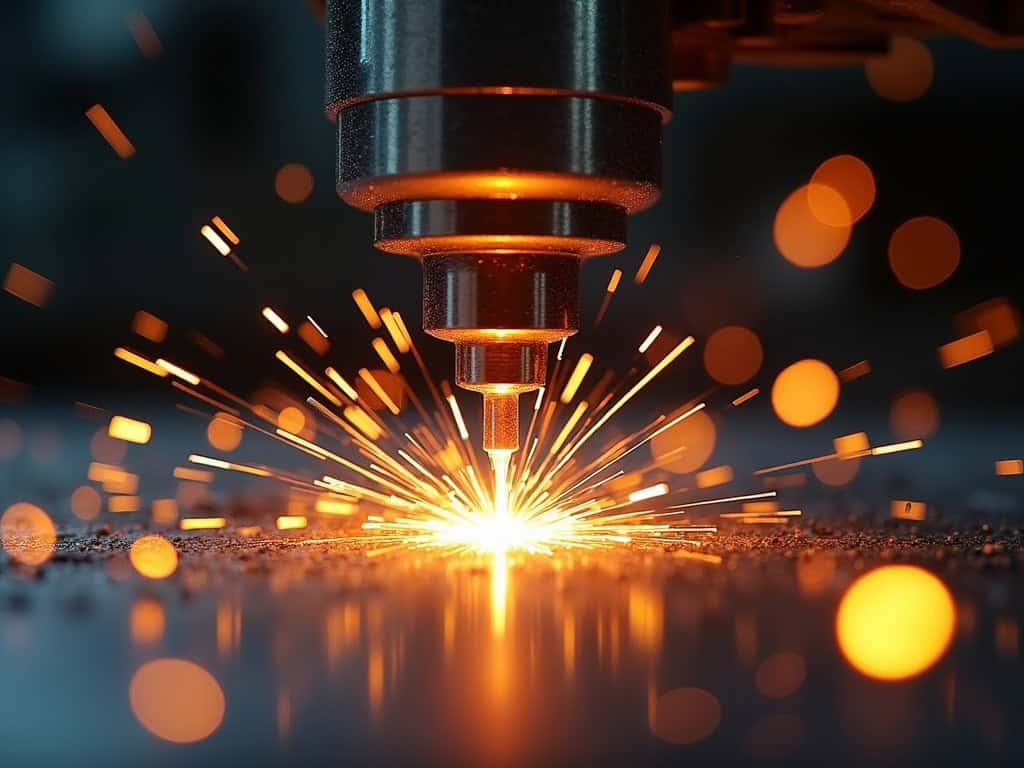
How EDM Works: The Basics
The EDM process involves two main components: the workpiece (typically made of conductive material) and the electrode (tool). The workpiece is connected to the positive terminal of a DC power supply, while the electrode is connected to the negative terminal, making the workpiece the anode and the electrode the cathode[3].
The workpiece and electrode are submerged in a dielectric fluid, usually hydrocarbon oil or deionized water. A small gap, called the spark gap, is maintained between the electrode and workpiece, typically ranging from 0.05 to 0.25 mm[2].
When the power supply is activated, the electrode generates a series of rapid, controlled electrical sparks. These sparks travel through the dielectric fluid and strike the workpiece, generating extremely high temperatures (8,000°C to 12,000°C)[3]. The intense heat melts and vaporizes tiny portions of the workpiece, gradually shaping it to the desired form.
Types of EDM
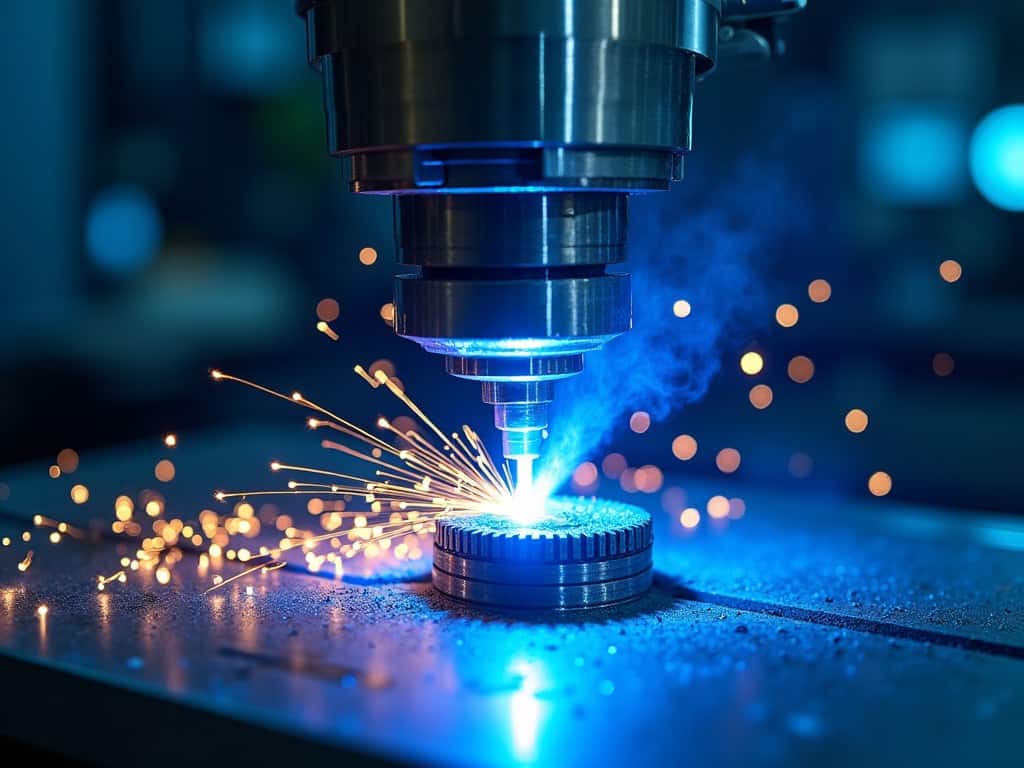
EDM encompasses three primary types, each with its unique features and applications:
Sinker EDM (Ram EDM)
- Uses a custom-shaped electrode that “sinks” into the workpiece
- Creates intricate 3D cavities and blind holes
- Ideal for mold and die making, particularly in the automotive industry[5]
Wire EDM
- Employs a thin, continuously fed wire electrode
- Excels at precise cutting of complex 2D profiles
- Used for high-tolerance parts in aerospace, microelectronics, and medical devices[5]
Small Hole EDM
- Utilizes a rotating tubular electrode
- Drills small, deep holes in tough materials
- Commonly used for creating cooling holes in turbine blades[2]
Advantages of EDM
EDM offers several key advantages over traditional machining methods:
- Precision and Accuracy: EDM can achieve tight tolerances (±0.0001 inches) and produce complex geometries with excellent repeatability[1].
- Material Versatility: EDM can machine hard, conductive materials like titanium, tungsten, and hardened steel that are difficult to process with conventional methods[4].
- No Mechanical Stress: Since there is no physical contact between the electrode and workpiece, EDM minimizes mechanical stress and eliminates the risk of tool breakage[1].
- Burr-Free Finish: EDM produces smooth, burr-free surfaces, often reducing or eliminating the need for additional finishing processes[1].
Applications of EDM
EDM finds applications across various industries, including:
- Aerospace: Fuel injection nozzles, turbine blades
- Automotive: Molds and dies for injection molding
- Medical: Surgical instruments, implants
- Electronics: Micro-machining of PCBs and semiconductors
- Toolmaking: Precision cutting tools, punches, and dies
Conclusion
Electrical Discharge Machining is a powerful and versatile manufacturing process that has transformed the way complex and high-precision components are produced. By harnessing the power of electrical sparks, EDM can machine intricate geometries in hard-to-work-with materials, offering unparalleled accuracy and surface finish.
As technology advances, EDM continues to evolve, with improvements in precision, efficiency, and automation. Understanding the principles and applications of EDM is crucial for engineers, designers, and manufacturers looking to push the boundaries of what’s possible in modern manufacturing.
Whether you’re creating complex molds, precision aerospace components, or intricate medical devices, EDM is a valuable tool in your manufacturing arsenal. By leveraging the unique capabilities of this innovative process, you can bring your most challenging designs to life with unmatched precision and quality.