Electrical Discharge Machining (EDM) is a cutting-edge manufacturing process that’s transforming the way we create complex, high-precision parts. Unlike traditional machining methods that rely on physical contact, EDM harnesses the power of electrical sparks to shape materials with incredible accuracy. This innovative technique has become a game-changer in industries ranging from aerospace to medical device manufacturing.
Key Takeaways |
---|
EDM uses electrical sparks to remove material |
Achieves high precision (±0.012mm) and complex shapes |
Ideal for hard, conductive materials like titanium |
Three main types: Die Sinking, Wire, and Hole Drilling EDM |
Best for low-volume, high-precision projects |
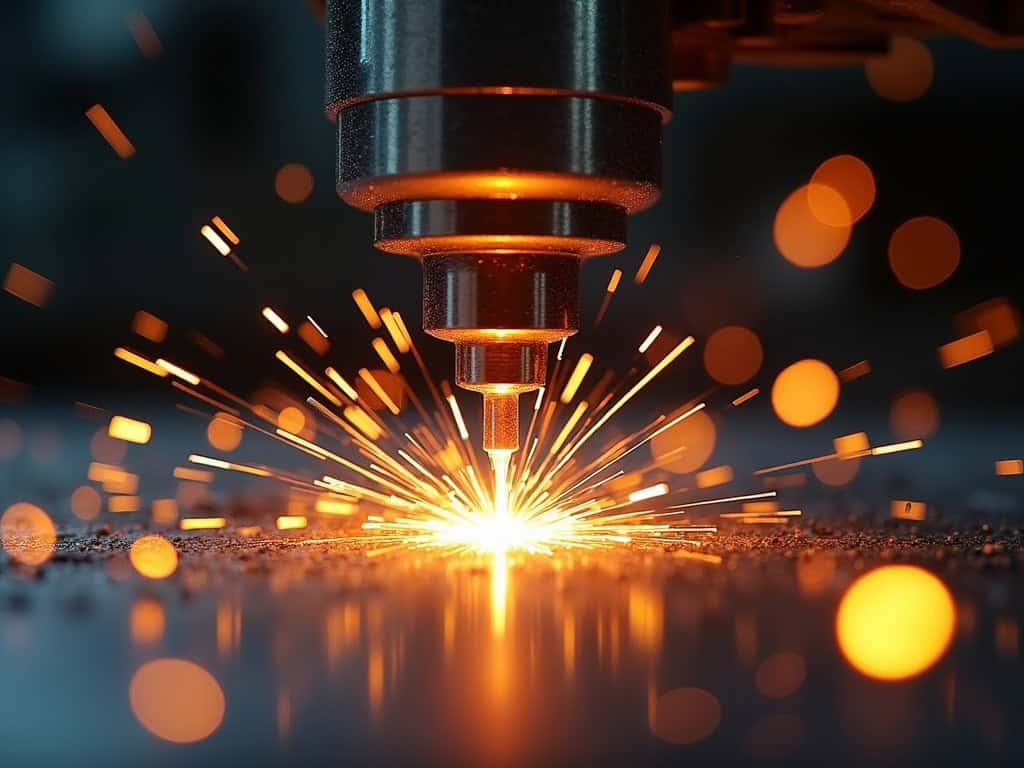
The Magic Behind EDM
At its core, EDM is all about harnessing the power of electricity to shape metal. Here’s how it works:
- The Setup: A workpiece (the material to be shaped) is submerged in a dielectric fluid.
- The Spark: An electrode is brought close to the workpiece, creating an electrical discharge.
- The Erosion: This spark, reaching temperatures of 8,000-12,000°C, vaporizes tiny bits of the workpiece.
- The Flush: The dielectric fluid carries away the eroded material and cools the area.
This process repeats thousands of times per second, gradually shaping the workpiece with incredible precision. It’s like watching a lightning storm in miniature, with each spark sculpting the metal to perfection.
Types of EDM: A Tool for Every Job
EDM isn’t a one-size-fits-all solution. There are three main types, each with its own strengths:
- Die Sinking EDM: Imagine pressing a custom-shaped electrode into metal like a stamp into clay. That’s die sinking EDM in a nutshell. It’s perfect for creating complex cavities and molds.
- Wire EDM: Picture a super-thin wire slicing through metal like a hot knife through butter. Wire EDM can create intricate 2D shapes with amazing precision.
- Hole Drilling EDM: Need a perfectly straight, deep hole in a tough material? Hole drilling EDM is your go-to, using a rotating electrode to bore through even the hardest metals.
Each type of EDM has its place in the manufacturing world, and choosing the right one can make all the difference in your project’s success.
The EDM Advantage: Precision Meets Possibility
EDM isn’t just another manufacturing method – it’s a problem-solver for engineers and designers. Here’s why it’s become so crucial:
- Unmatched Precision: EDM can achieve tolerances as tight as ±0.012mm. That’s about a quarter of the width of a human hair!
- Complex Shapes: Need an internal corner with a sharp 90-degree angle? EDM can do that, no problem.
- Hard Materials: Titanium, Inconel, hardened steel – EDM tackles materials that would make traditional cutting tools cry.
- No Mechanical Stress: Since there’s no physical contact, there’s no risk of distorting delicate parts during machining.
For example, when creating precision tool sets, EDM can produce components with the exacting standards required for high-performance tools. Similarly, in the automotive industry, EDM is often used to create complex mold cavities for injection-molded parts, ensuring perfect fit and finish.
The Limits of EDM: When to Look Elsewhere
As magical as EDM may seem, it’s not the answer to every manufacturing challenge. Here are a few situations where other methods might be a better fit:
- High Volume Production: EDM is a relatively slow process, so it’s not ideal for churning out large quantities of parts. For mass production, techniques like CNC machining or injection molding are often more efficient.
- Non-Conductive Materials: EDM only works with materials that can conduct electricity. So if you’re working with plastics, ceramics, or other non-conductive materials, you’ll need to find another solution.
- Large Parts: While EDM can handle pretty big workpieces, there are limits. If you’re dealing with truly massive components, you might need to explore other options.
It’s all about choosing the right tool for the job. Just like you wouldn’t use a mini chainsaw to fell a giant oak tree, you wouldn’t use EDM for every manufacturing project.
The EDM Process: A Delicate Dance
Getting the most out of EDM requires a deep understanding of the process parameters. Here are a few key factors that can make or break your results:
- Electrode Material: The electrode is the tool that shapes the workpiece, so choosing the right material is crucial. Graphite and copper are popular choices, each with its own strengths and weaknesses.
- Dielectric Fluid: This liquid medium is the unsung hero of EDM, providing insulation, cooling, and debris removal. The type of fluid can have a big impact on cutting speed and surface finish.
- Spark Gap: The distance between the electrode and workpiece is critical. Too close, and you’ll get uncontrolled sparking. Too far, and you won’t get any sparks at all. Finding the sweet spot takes skill and experience.
Mastering these variables is what separates the EDM novices from the pros. It’s a delicate dance of science and art, requiring a keen eye and a steady hand.
EDM in Action: From Aerospace to Medical Devices
The versatility of EDM has made it a go-to solution across a wide range of industries. Here are just a few examples:
- Aerospace: EDM is often used to create complex fuel injection nozzles, turbine blades, and other high-precision components for aircraft engines.
- Medical Devices: From surgical instruments to implantable devices, EDM’s ability to create tiny, intricate parts with smooth surfaces makes it a natural fit for the medical industry.
- Automotive: EDM is commonly used to create molds for injection-molded parts, as well as precision components for engines and transmissions.
- Electronics: The tiny, complex parts required for modern electronics are often made using EDM, thanks to its ability to create fine details and tight tolerances.
Whether you’re building a rocket engine or a smartphone, there’s a good chance EDM has played a role in bringing your vision to life.
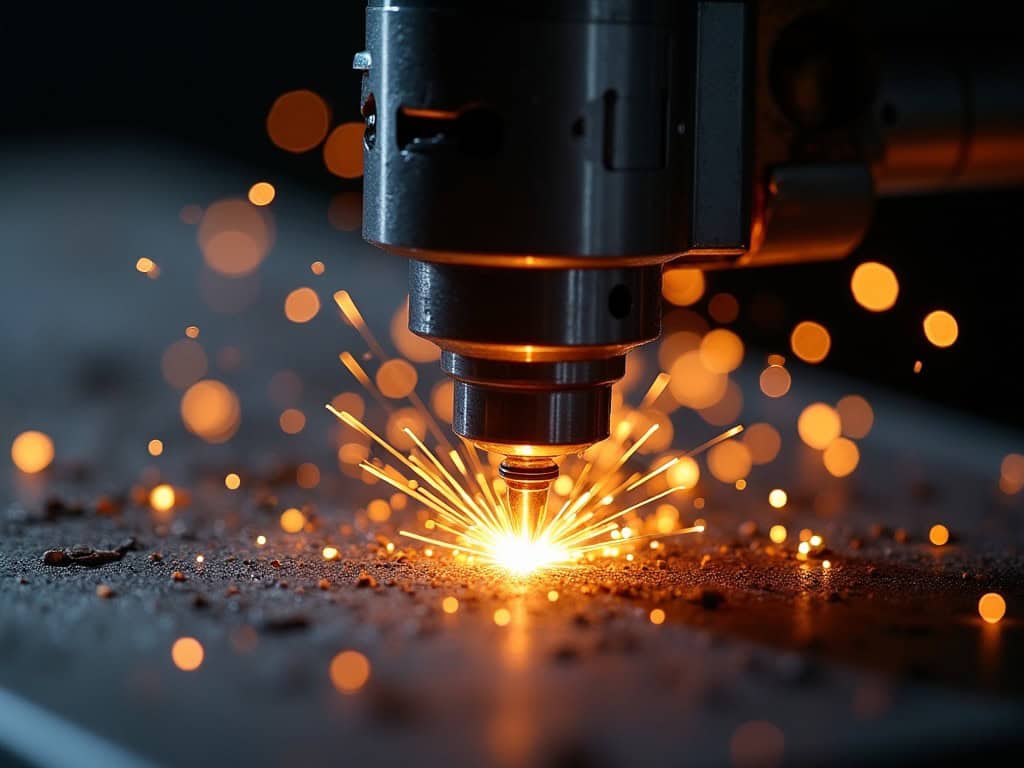
The Future of EDM: Pushing the Boundaries
As technology continues to advance, so does the potential of EDM. Here are some exciting developments on the horizon:
- Micro-EDM: This technique is pushing the limits of miniaturization, allowing for the creation of parts with features as small as 5 microns – that’s about 1/20th the width of a human hair!
- Hybrid Machines: Combining EDM with other machining techniques in a single machine is opening up new possibilities for efficient, multi-step manufacturing processes.
- AI and Machine Learning: These technologies are being applied to optimize EDM processes, predicting optimal parameters and reducing setup time.
The future of EDM looks bright, with innovations promising even greater precision, efficiency, and capabilities.
DIY EDM: Is It Possible?
While professional EDM machines can cost hundreds of thousands of dollars, there’s a growing community of DIY enthusiasts experimenting with homemade EDM setups. While these DIY solutions can’t match the precision of professional equipment, they offer a fascinating way to explore the principles of EDM.
If you’re interested in trying your hand at EDM, here are a few tips:
- Start Small: Begin with simple projects and gradually work your way up to more complex ones.
- Safety First: EDM involves high voltages and potentially hazardous materials. Always prioritize safety and follow proper guidelines.
- Learn the Basics: Understanding the fundamentals of electricity and machining will go a long way in your EDM journey.
Remember, even if you’re not ready to dive into DIY EDM, you can still apply EDM principles to other projects. For example, when working on precision tool sets, understanding the importance of tight tolerances and surface finish can help you choose and use your tools more effectively.
Conclusion: The Spark of Innovation
Electrical Discharge Machining has revolutionized the world of precision manufacturing, enabling the creation of parts that were once thought impossible. From the tiniest components in your smartphone to critical parts in jet engines, EDM plays a crucial role in shaping the modern world.
As we’ve explored, EDM is not without its limitations. It’s not the fastest or cheapest manufacturing method, and it’s not suitable for every material or project. But when it comes to creating complex, high-precision parts from tough materials, EDM is often the best – and sometimes the only – solution.
Whether you’re a professional engineer, a DIY enthusiast, or simply someone curious about how things are made, understanding EDM offers a fascinating glimpse into the cutting edge of manufacturing technology. It’s a reminder that sometimes, the most powerful tools aren’t the ones that cut or grind, but those that harness the fundamental forces of nature in new and innovative ways.
So the next time you’re using a precision tool set or admiring the sleek design of your smartphone, take a moment to appreciate the invisible sparks of EDM that might have played a role in bringing these marvels to life. In the world of manufacturing, sometimes the most impressive feats are accomplished not with brute force, but with the careful, controlled power of a tiny electrical spark.
1 thought on “EDM Machining: Revolutionizing Precision Manufacturing”